If you talk with someone about inventory long enough, chances are, ABC codes will become a topic of discussion. This simple idea can have a major impact on various parts of your inventory management program, from purchasing to cycle counting.
What is ABC Analysis?
ABC Analysis is a method with which you can segment inventory to better manage not just the items, but the time spent working with inventory. To accomplish this, you should first assign each item an A, B, or C. Each letter will represent a predefined segment of inventory which will then determine how you and your team interact with it.
- Category A:
This will be the category with the fewest total SKU count but will also represent the largest percentage of your annual consumption. The idea behind this category is to have all the high-impact items categorized together. Category A is typically 20% of your inventory SKUs, making up about 70% of your annual consumption. - Category B:
This category is often the most difficult to identify as it becomes a mixed bag of items that move frequently. In addition, these items may tend to move a little slower. Category B is typically 30% of your inventory SKUs, making up about 25% of your annual consumption. - Category C:
This will be the largest category from an item standpoint but will represent the smallest percentage of consumption. The items in this category are low impact in terms of value, but that doesn’t mean the parts aren’t necessary for day-to-day business. This category typically has a high number of spare and replacement parts, as well as one-off purchased items. Category C is typically about 50% of your inventory SKUs but only accounts for the last 5% of your annual consumption.
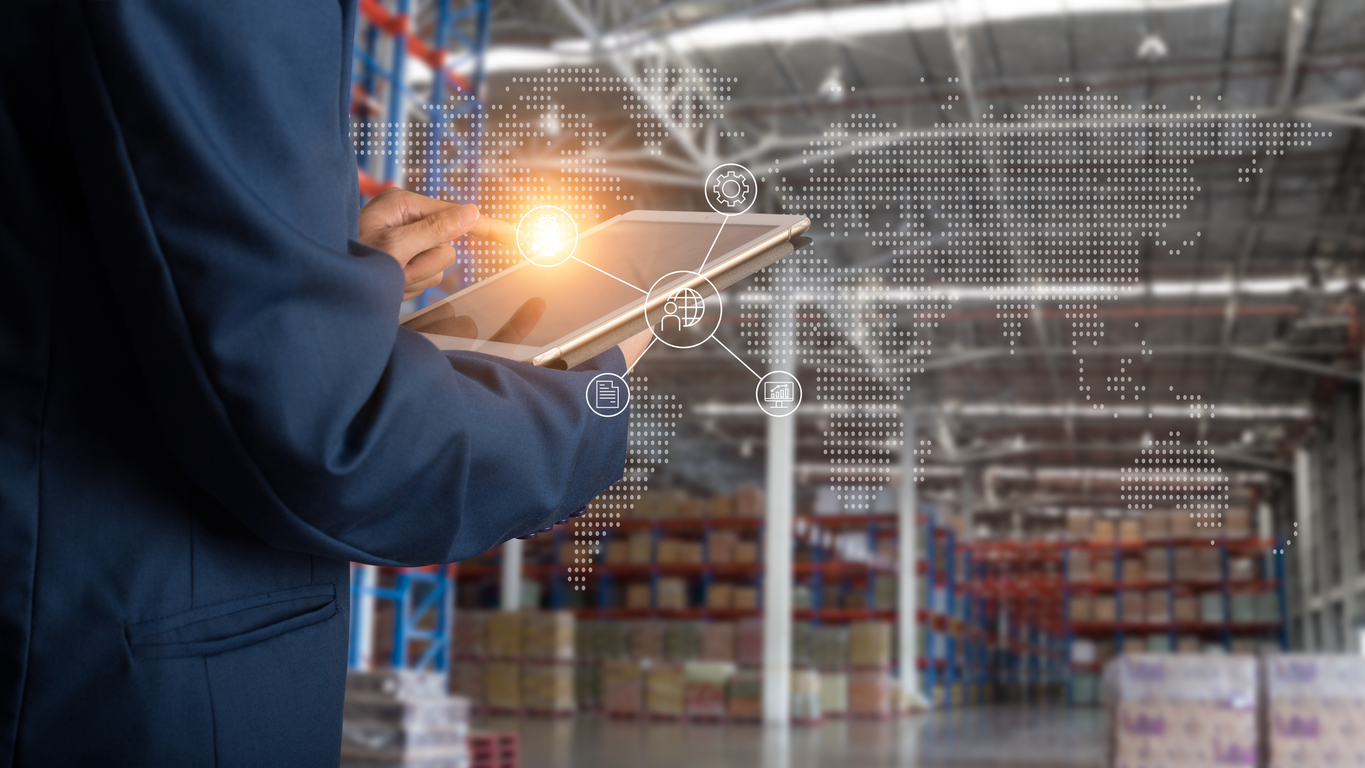
How Can I Use This in My Inventory
Once your inventory has been categorized, what are some ways in which this can be used? Most often, ABC codes are used in purchasing and inventory control.
From a purchasing standpoint, ABC codes can offer a different perspective on how to manage orders from a higher level. Instead of using the same method to order your entire inventory, a better focus can be used with each category. With Category A parts, it typically makes sense to employ the most oversight, verifying costs, lead times, and correctness of purchase orders. Since these parts have such an impact on your inventory’s bottom line, it is prudent to be methodical about ordering them. Category B parts can sometimes act like A parts, so perhaps having a higher stock level would make sense. This would alleviate any expedited shipping costs in emergencies, and with the low number of items overall, the financial impact wouldn’t be high. Category C parts are usually happiest on a minimum/maximum with lean stocking levels. It isn’t practical to stock large quantities of each item, as C parts are the largest category and most storerooms have limited space.
Another great way to utilize ABC codes is for cycle counting. Incorporating the ABC code into your cycle count process will add a layer of control and efficiency. Much like the percentages used when determining the A, B, and C categories, A items will be counted most often as their accuracy is paramount to daily business, B items less frequently, and even less so C items. Using a yearly cycle count process, A items would be counted weekly, B items monthly, and C items just once a year.